R&D
Pursuit of technology
for a sustainable society
The businesses of Toho Titanium have developed widely based on our ceaseless efforts to develop new technologies and these technologies have been created by ourselves. R&D in Toho responds to the apparent demand from customers and contributes to the development of a sustainable society by the new processes and products that can reduce the environmental load.
01Contributing to a recycling society with LLTO™
Recovering and recycling lithium resources with LLTO™
Making effective use of resources and contributing to a recycling society
The increasingly widespread use of EVs and renewable energy storage systems is expected to reduce CO2 emissions. Developed for use in recovering solid electrolytes for lithium ion batteries (LIBs) and lithium resources, LLTO™ can contribute particularly to lithium recycling by recovering lithium resources directly from waste LIBs, whose volumes are expected to grow, using electrodialysis (direct lithium extraction).
Click here, for details on LLTO™
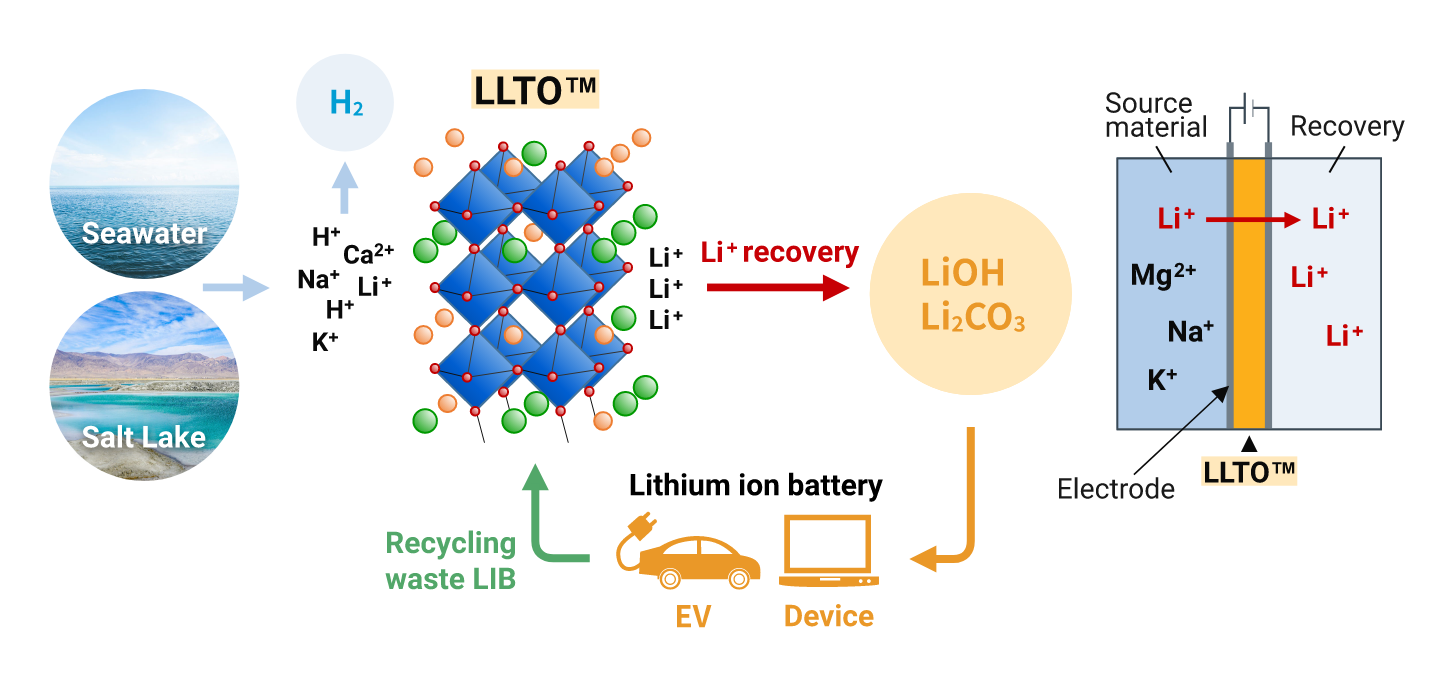

Lineup of LLTO™ products
■ LLTO™ plate
Form | Size |
---|---|
Square plate | 0.5-3.0 mm thick × 10-50 mm square |
Circular plate | 0.5-3.0 mm thick × φ10-30 mm |
※Please contact us if requiring dimensions of 100mm square or greater.
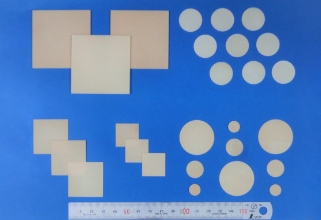
■ Lineup of LLTO™ products
Product name | TP-02N (ordinary product) |
TP-02F (pulverized product) |
TP-10F (pulverized product) |
---|---|---|---|
Specific surface area | 1.4m2/g | 2.5m2/g | 10.4m2/g |
Tap density | 1.4g/cm3 | 1.5g/cm3 | – |
LLTO is a trademark of Toho Titanium Co., Ltd.
02Contribution to a hydrogen society with porous titanium
To utilize porous titanium sheets for hydrogen production equipment
We developed WEBTi®, a porous titanium metal sheet with a lot of micropores. “WEBTi®” is a new material that has both the characteristics of porous metal such as liquid permeability and conductivity and the features of titanium such as high corrosion resistance. We assume that it will be used for electrode materials, diffusion layers, filters and etc. in a severe corrosive environment. Nowadays, it is expected to be used for the anode-side diffusion layer of a water-electrolysis hydrogen generator with polymer electrolyte membranes (PEMs). A water-electrolysis is indispensable for realizing a hydrogen society which is one of the promising approach for reducing CO2. We will practically apply WEBTi® to PEM water-electrolysis as soon as possible, to contribute to the reduction of CO2.
WEBTi®-K –porous titanium sheet–
Appearance
Surface (SEM)
PEM water electrolyzer (Hydrogen production equipment)
03Significant omission of the production process of titanium foil
Direct manufacturing of titanium foil with electro-deposition
At present, titanium foil is produced through a lot of processes, including the melting of raw material, casting, hot rolling and multiple cold rolling. In the new process under development, production processes are significantly omitted because raw materials deposit directly in the foil form by electro-deposition in molten salt. Since electro-deposition has refining effects, inexpensive titanium scrap can be used as a raw material. Accordingly, it is expected to contribute to the saving of energy and resources.
The titanium foil produced through this process could be used for the bipolar plates of a water-electrolysis hydrogen generator with PEMs, corrosion-proof films of steel structures, etc. By using it, we could contribute to the reduction of CO2 and the maintenance of social infrastructure.
Mechanism of smooth electro-deposition of titanium foil
Deposited titanium foil of the A4 size
04Simplification of machining process with near net shape
Development of titanium alloy components with the powder blending and compression method
The workload and loss of material in machining process are one of the challenges for manufacturing of complex shaped parts made of titanium alloys because titanium alloys are relatively expensive and difficult to machine. We have developed the near net shape manufacturing technology with the “powder blending and compression method,” in which pure titanium powder and master-alloy powder are mixed, put into a mold, compressed and sintered to produce alloy parts. While this technology had existed from the past, we can easily produce materials in complex shapes by adopting resin molds made with a 3D printer. By this near net manufacturing process, it is expected that titanium alloy parts in various shapes are manufactured efficiently even in small lots and loss of materials is reduced.
■ Flowchart of the processes under development
Sintered material
Compressed powder
The titanium world, which is expanding
while looking ahead to future possibilities.
Titanium is being applied in a broader range of fields, because its potential as a material has been recognized.
We will make continuous efforts to make titanium used in a broader range of fields, in cooperation with clients.